Scrubbers and Ballast Water Systems for Superintendents and Ship Managers – InterManager and BEMA Conference
21.03.2019
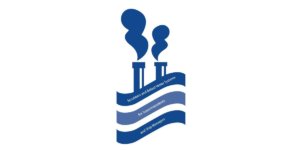
13.04.2019 Scrubbers and Ballast Water Systems for Superintendents and Ship Managers – InterManager and BEMA Conference @ Columbia Plaza, Limassol
The conference was opened by its chair – Cpt. Kuba Szymanski. He warmly greeted the guests and circled the main topics of conference – scrubbers and ballast water management installation. He reminded that the Marine Environment Protection Commitee (MEPC) confirmed in July 2018 that the new global sulphur limit for marine fuel of 0,50% m/m will apply from 1 January 2020. Further, amendments to MARPOL Annex VI which prohibit vessels from carrying fuel oil with sulphur content of more than 0,5% m/m have been apso approved by IMO.
Such measures will come into force on 1 March 2020, after which only vessels which are equipped with Exhaust Gas Cleaning System will be exempt from this prohibition.
The first session consisted of two speeches. The first one was made by Mr. John Doherty, v-ce President of sales of Know-NOx- LLC, american based company which is engaged in commercializing the technology developed by Pacific Rim Design & Development with HQ in Nevada USA and Development Lab in Northern CA USA.
Know-NOx is a combined SO2 and NOx scrubbing system. Both pollutants are treated with the same equipment. The system will treat exhaust from any existing marine fuel (MGO, HFO, Bunker oil). To scrub the exhaust the device is using Chlorine dioxide – the same certified chemical that is now approved for ballast water treatment.
He stressed that marine industry is addressing the environmental problems by initially regulating SO2 and NOx as a step toward addressing Global Warming Gas emissions. The shipping industry is joining the effort to ensure global seawater warming remains less than 2o C. It was stated that both gas don’t really impact Global Warming so much but they do make acid rain and contribute to smog.
The second speech was made by Mr. John Lee, Marking Director at Shandong Pure Ocean Technology Co Ltd. He introduced the history of the company, which is a very young player on the scrubbers market. The company was established in 2017. It’s mainly engaged in the production and sales for Exhaust Gas Cleaning System. His attention was focused on two types of scrubbers – I-Type and U-Type, in three variants of work (open, closed and hybrid). The installation is made on special super duplex stainless steel. Its capacity is designed based on the maximum treated exhaust gas volume.
Open loop mode uses sea water as the wash water to clean the exhaust gas. This simple makes use of the natural alkalinity of the sea water pH is 7.8 up to 8.3 in chemical absorption of the SOx. The treated exhaust gas can be released to the environment, and the effluent is also discharged in compliance with IMO requirements. Open loop mode applies to our of ECA
zone and open sea and 200 sea miles from land.
Closed loop moge uses sea water or fresh water as the wash water. This mode is applied in low alkalinity of fresh water area. High concentration of NaOH is added to obtain a certain DeSOx capacity. The wash water is recycled and capable of zero discharge requirement. The power is less than that of open loop mode. Closed loop applies to zone withis ECA and open sea.
Hybrid mode is the combination of open and closed loop modes. In this mode, it is possible to switch between these two process depending on the condition of sea water alkalinity and discharge restrictions etc. During open sea navigation, it would typically operate in open loop made to reduce caustic NaOH and wash water consumption. White close to port or ECA, it would typically operate in closed loop mode. This mode provides high flexibility and enables customers to choose the best solution both economically and technically.
Owners of large vessels with operating profiles that involve the majority of time that involve the majority of time steaming on open water are likely to find that these vessels will benefit from installing a scrubber. If, however, an owner has a vessel that has a low power output and spends a higher proportion of its time in Emission Control Areas or port, then it is likely a scrubber is not the best choice, unless they consider installing a hybrid system that would allow the vessel to operate in these areas without fear of compliance issue both now and in the future. Mr. Lee stressed that the most important thing in planning of scrubber installation is space. For example most passengers vessels are forced to install scrubbers in the funnel space.
After the lunch, the second part of conference was started. The main subject – ballast water management system.
Now few words about balast water convention. Since the introduction of steel-hulled vessels, water has been used as ballast to stabilize vessels at sea. Ballast water is pumped in to maintain safe operating conditions throughout a voyage. This practice reduces stress on the hull, provides transverse stability, improves propulsion and manoeuvrability, and compensates for weight changes in various cargo load levels and due to fuel and water consumption.
While ballast water is essential for safe and efficient modern shipping operations, it may pose serious ecological, economic and health problems due to the multitude of marine species carried in ships’ ballast water. These include bacteria, microbes, small invertebrates, eggs, cysts and larvae of various species. The transferred species may survive to establish a reproductive population in the host environment, becoming invasive, out-competing native species and multiplying into pest proportions. For that reason IMO take carte of that. The result was Ballast Water Management Convention which step into force on 8th September 2017.
The International Convention for the Control and Management of Ships’ Ballast Water and Sediments requires ships to manage their ballast water to remove, render harmless, or avoid the uptake or discharge of aquatic organisms and pathogens within ballast water and sediments.
The list of speechers was much longer than in morning sessios, we got:
1. Debra DiCianna, Senior Compliance Engineer, Choice ballast Solutions
2. Dr Vladomiro Bonamin, v-ce President, SGS Geneva
3. Marcie Merksamer, Secretary-General, BEMA and v-ce President EnviroManagement Inc
4. Tom Perlich, Managing Director, Ecochlor
5. Andreas Zontanos, Partner, Argo Navis
6. Jurrien Baretta, Technical Sales Manager, Optimaris AS
All the above mentioned participants were introducing its sales products – balast water system. During this part the delegates discussed about the process and considerations for succesfull BWTS retrofit installation. Very specialized and technical knowledge was provided to the listeners. I refer all interested parties to visit the websites of the above mentioned producers.
A very interesting speech about commissioning proccess was delivered by Mr. Vladimiro Bonamin. Project commissioning is the process of assuring that all systems and components of a building or industrial plant are designed, installed, tested, operated, and maintained according to the operational requirements of the owner or final client. A commissioning process may be applied not only to new projects but also to existing units and systems subject to expansion, renovation or revamping.
In practice, the commissioning process comprises the integrated application of a set of engineering techniques and procedures to check, inspect and test every operational component of the project, from individual functions, such as instruments and equipment, up to complex amalgamations such as modules, subsystems and systems.
Commissioning activities, in the broader sense, are applicable to all phases of the project, from the basic and detailed design, procurement, construction and assembly, until the final handover of the unit to the owner, including sometimes an assisted operation phase.
The conference has ended.